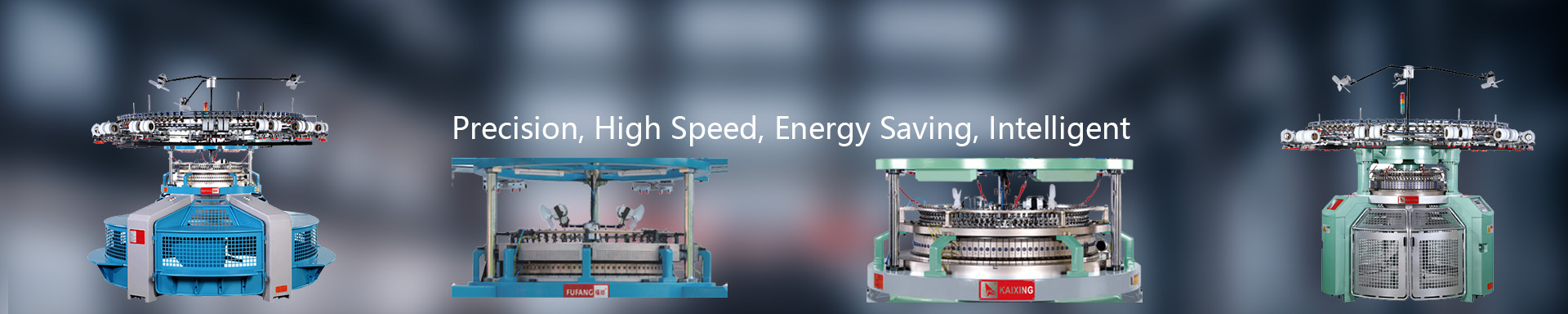
How does a circular knitting machine work?
2022-12-01 22:00In the loop forming process, the yarn forms a loop, which becomes a knitted fabric through longitudinal interlocking and transverse connection. So looping is the basic process of knitting. The knitting process can be decomposed into the following stages in sequence: unknitting - moving the newly formed loop (called the old loop) from the needle hook to the needle bar; laying yarn - feeding the yarn to the knitting needle; bending the yarn ——Bend the yarn into the shape of a thread Tape yarn——Move the new yarn on the pad or the newly bent loop to the inside of the hook and close it—Close the needle mouth loop——Place the old loop on the needle mouth On a closed hook.
Coil--new yarn or new coil and old coil meet inside and outside the needle hook and de-coil--the old coil is taken off the needle hook and put on the new coil; looping-making the yarn form a closed loop and a new coil of the specified size; pull--pull the new coil away from the coiling area. This new coil becomes the old coil in the next coil forming cycle. There are two types of knitting and knitting in the loop forming process. During the knitting process of knitting, each stage of knitting is carried out in the above order. In the knitting process of the knitting method, the yarn bending begins with the knocking off and is carried out simultaneously with the knitting stage. On some knitting machines, each knitting needle completes the knitting process sequentially, and the knitting process of some knitting machines is carried out simultaneously by each knitting needle in a whole row.
In knitting production, in addition to weaving various gray cloths, cutting and sewing various knitted products, it can also directly weave shaped products on the machine to make fully formed or partially formed products. The forming process can save raw materials, simplify or cancel the cutting and sewing process, and improve the wearability of the product. Knitting production has developed rapidly due to its short process, strong adaptability of raw materials, quick change of varieties, wide range of products, low noise and low energy consumption. Since the 1970s, the productivity of knitting machines has been greatly improved. For example, circular weft knitting machines (latch needles) can weave about 3,000 coil rows per minute, and the weaving width of warp knitting machines is mostly 427 cm. It can knit 2,000 stitches and rows, and the maximum speed of the single-cylinder circular hosiery machine can reach 1,000 revolutions per minute.
The use of electronic technology to control the work of the knitting machine improves the efficiency of the machine. The quality of the product can be improved by installing various positive yarn feeding devices on the machine. Adding some mechanisms to the machine can weave knitted fabrics with various organizational structures and different uses: for example, using a needle selection mechanism to make the knitting needles work according to a pre-arranged program to weave jacquard knitted fabrics; using a carding mechanism to feed loose fibers into the fabric The needle is used to weave plush knitted fabrics and the warp and weft insertion device is used to weave warp and weft inserted knitted fabrics. There are many kinds of knitting machines, more than 350 kinds. With the development of new varieties of chemical fibers and finishing processes, the characteristics of knitted fabrics such as scratch resistance, non-ironing and wear resistance have been improved. The application of finishing techniques such as brushing, sanding, shearing, embossing and pleating has expanded the variety of knitted products.